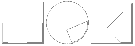
Zimmerei Johannes Wagner
Adresse: Am Industiegelände 20, 13591 Berlin
Die Holzbaufirma Johannes Wagner ist spezialisiert auf traditionelle Zimmerei-Arbeiten. Sie befindet sich in Berlin-Staaken auf dem Gelände des ehemaligen Flugplatzes.
Die Zimmerei wurde bereits 1925 gegründet, wuchs allmählich und befindet sich inzwischen an ihrem dritten Standort.
1962 übernahm Hr. Blaese die Firma, die heute die größte Zimmerei Berlins ist. Zurzeit sind 40 Mitarbeiter beschäftigt und 12 Lehrlinge befinden sich in Ausbildung.
Beeinflusst durch seine persönlichen Erfahrungen während seiner Lehrzeit möchte Hr. Blaese heute jungen Menschen die Möglichkeit eines Ausbildungsplatzes bieten. So haben im Laufe der Jahre 120 Gesellen ihre Prüfung im Betrieb bestanden, d.h. etwa vier pro Jahr.
Früher war die Zimmerei Wagner war sehr handwerklich ausgerichtet, aber unter den heutigen ökonomischen Bedingungen bestand die Notwendigkeit, die Logistik wirtschaftlicher zu gestalten.
Mit dem Einsetzen der Wirtschaftskrise 1994/95 und dem daraus entstehenden Wettbewerb begann der Kampf um den Erhalt der Mitarbeiter. Heute gibt es Aufträge über Alternativen, die J. Wagner GmbH bietet beispielsweise Beratungsleistungen für wirtschaftlichere Lösungen an und erst bei der Ausschreibung erfolgt der Einstieg ins Bauvorhaben. Die meisten Projekte sind Einzelaufträge und ergeben sich hauptsächlich über Empfehlungen von Architekten und Bau-Ingenieuren, die bereits mit der Zimmerei zusammengearbeitet haben.
Die Johannes Wagner GmbH führt alle Arbeiten im Berufsbild des Zimmerhandwerks aus:
- klassische Zimmermannsarbeiten
- moderne Holzständerbauwerke
- Ingenieurbauweise BSH
- freitragende Konstruktionen
- Restaurierung
- Hallenbau
Besonders viel Gewicht liegt auf der Ausführung von Restaurierungen, so wurden beispielsweise das Neue Palais, das Schloss Köpenick, diverse Kirchtürme und das Elefantentor am Zoo restauriert. Momentan baut die J. Wagner GmbH die Westernstadt in Templin.
Das Leistungsspektrum der Firma wird definiert von 70-80 % gelernten Zimmerern und Zimmererhelfern. Besonders die Aufgaben in der Denkmalpflege sind hoch lohnintensiv.Der Umsatz richtet sich dabei nach dem Material- bzw. Lohnfaktor. Dabei hat sich durch den Bau von Fertighäusern kein Umsatzrückgang ergeben.
Der jährliche Umsatz beläuft sich auf 3 - 4 000 000 €.
Der Lieferumkreis erstreckt sich bis Leipzig, Dessau, Cottbus und bis zur polnischen Grenze.
Die Firma bezieht ihr Holz von vier festen Zulieferern, dabei kommt das Holz nicht nur aus Deutschland, sondern auch aus Polen, der Tschechei, aus Russland, Ungarn ... zum Beispiel die Rubinie oder die Schwarzkiefer.
Um unter den schärferen ökonomischen Bedingungen wettbewerbsfähig zu bleiben, entschloss man sich zum Neubau des heutigen Firmensitzes.
Dieses Gebäude muss verschiedenen Aufgaben gewachsen sein: es beherbergt die Fertigungshalle, die groß genug sein muss, um den Lastzug, der das Holz anliefert, komplett aufnehmen zu können. Dort wird es mit einem Kran abgesetzt, bearbeitet und erneut mit dem Kran oder Gabelstapler abtransportiert. Weiterhin befindet sich in der Halle eine moderne, computergestützte Abbundanlage. Im Mittelteil befinden sich die Büros und der Sozialbereich, der einen Aufenthaltsraum für alle Mitarbeiter mit einschließt.
Im rückwärtigen Teil des Gebäudes befinden sich ein gedecktes Lager und eine Tränkanlage zur Holzimprägnierung.
Das Gebäude wird ausschließlich mit der Verbrennung von Holzabfällen geheizt, im neben der Halle positionierten Silo läuft eine große Schnecke, die die Späne in den Kessel zieht.
In der Fertigungshalle steht noch die alte Abbundanlage, die hydraulisch gesteuert ist und eine Reihe von Werkzeugen wie Kreissägen und Fräsköpfe beherbergt. Seit 2,5 Jahren ist nun die neue Abbundanlage in Betrieb. Die Investition in eine neue Anlage ist sehr hoch, ca. 300 - 350.000,- €. Mit der Abbundanlage (Standard-Ausrüstung von "Hundegger") lassen sich eigentlich alle zimmermannsmäßigen Verbindungen herstellen, so zum Beispiel Kehlbalken und Aufklauungen. Heute werden viele diese Verbindungen wieder eingeführt, da sie durch die maschinelle Fertigung wieder günstiger geworden sind.
Die Anlage ist computergestützt und läuft vollautomatisch. So müssen einfache Bauteile sogar nummeriert werden, weil die Maschine so schnell produziert.
Die Pläne der Auftraggeber werden in der Firma im dxf-Format abgegeben und dort wird mit eigener CAD-Software aus der Geometrie ein neuer Werkplan erstellt. Nach der PC-Vorgabe läuft das zu bearbeitende Holz auf Wagen bzw. Schienen bis zu der Position (geschützt durch eine Scheibe), an der von unten verschiedene Fräsen und Sägen hochfahren und die programmierten Schnitte ausführen. Die anfallenden Späne werden unterirdisch abgesaugt und zum Brennofen transportiert.
Die Fertigung in der Abbundanlage ist immer exakt und zwar millimetergenau.
Die Tränkanlage wurde trotz des Standortes in einem Wasserschutzgebiet genehmigt. Sie ist positioniert über einem Pumpensumpf, der geneigte Boden unter der Anlage besteht aus sehr dichtem Beton und die Anlage selbst hat eine doppelte Wanne.
Die Tränkanlage befindet sich im Außenbereich, da die verwendeten Borsalze giftige Dämpfe entwickeln. In ihr können Hölzer bis zu 12 m Länge (ab 12 m wird per Hand gestrichen oder gesprüht) mit einer Imprägnierung versehen werden. Die Tauchzeiten variieren je nach gewünschtem Ergebnis, welches durch einen zugesetzten Farbstoff kontrolliert werden kann. Unter der Tränkanlage ist eine Heizanlage, denn das außen gelagerte Holz ist durch seine Eigenfeuchtigkeit im Winter gefroren und muss erst aufgetaut werden, ab -10 °C gefriert selbst das Bor-Salz.
Im Imprägnierprozess setzt das Borsalz sich in die Zellen, die Eigenfeuchtigkeit zieht das Salz hinein, aus diesem Grund braucht trockenes Holz länger. Die Salzlösung in der Tränkanlage wird einmal jährlich ergänzt, da sich Späne absetzen.
Für die Imprägnierungen gibt es verschiedene Prüfzeichen |
P |
pilzwidrig |
IV |
insektenvorbeugend |
W |
wetterbeständig |
Neben der Imprägnierung ist beim Holzbau auch immer der konstruktive Holzschutz zu bedenken, so ist beispielsweise die Außenstütze des gedeckten Lagers mit einem Stahlschuh vom Boden abgehoben, um Schäden durch Wasser zu verhindern. Für eine Außenfassade eignet sich Zeder, deren Holz ist so ölhaltig, dass es nicht imprägniert werden muss, für Lärche gilt das gleiche, wenn auch etwas eingeschränkt.
Imprägniert werden Kiefer, Fichte, Douglasie wobei sich das Spätholz anders verhält als das Frühholz. Die Oberfläche wird rau, deshalb ist Salz weniger geeignet und das Holz muss mit lösungsmittelhaltigen Imprägnierungen oder mit Ölen behandelt werden. |